电动汽车电池箱到底是如何设计的,其内部构造要还有优化空间吗?

文 | 法老
编辑 | 法老
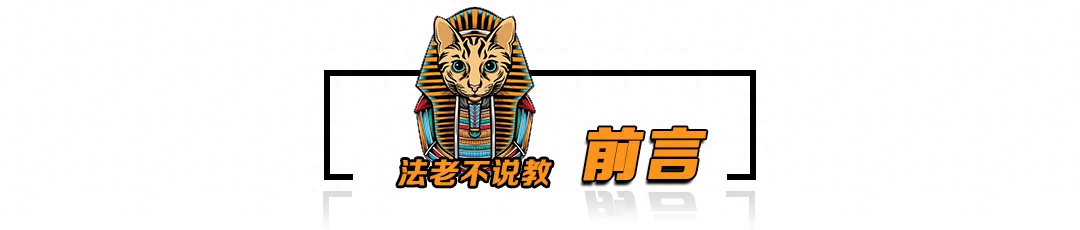
电池系统是电动汽车的唯一能量来源,它的性能对电动汽车的安全性、可靠性等有着:至关重要的影响。
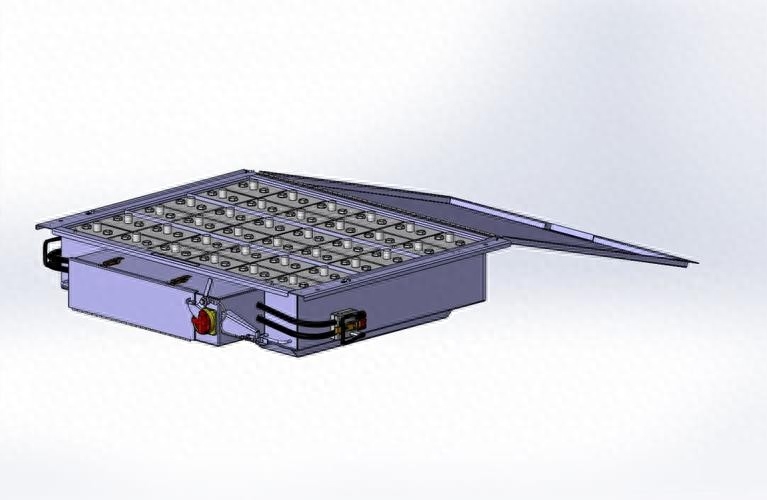
电池箱是电池系统的重要组件,在保护电池方面有着不可替代的作用,同时电池箱对整车通过性和稳定性也有一定影响。
传统的试制方法尽管可靠性强,但是存在设计周期长、成本高、安全余量过大等问题;

随着有限元技术的成熟和数值计算方法的发展,有限元分析在汽车制造领域的应用越来越广泛。
那么,电池箱到底是如何设计的,其内部构造要还有优化空间吗?我们如何改进才能为后续的轻量化设计提供优化基础?
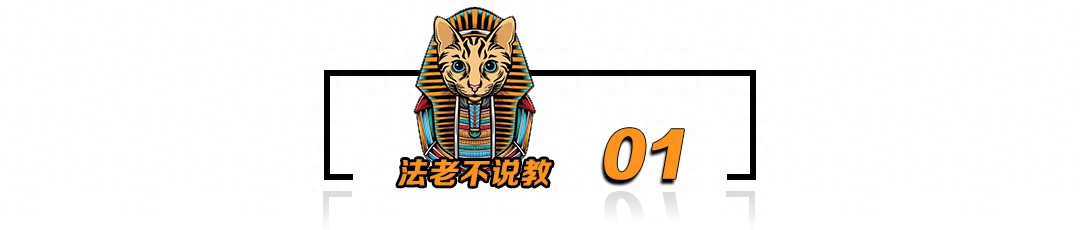
电池系统具有很大质量,它在整车中的位置,直接影响汽车的安全性和操纵稳定性。
一般情况下,电池箱的空间大小和布置位置都是根据整车的空间设计决定的。因此在电动汽车开发时,就应该考虑合理的布置方案。
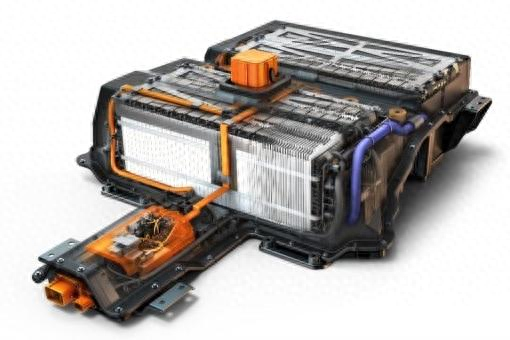
电池箱的布置因素主要包括:整车的轴荷分配、整车的最小离地间隙、电动汽车的驱动形式、整车空间、电池系统的冷却方式等。
现在的纯电动汽车中有一部分是在传统汽车的平台上开发的,所以电动汽车的电池布置形式各种各样,表3.1总结了电池箱不同布置方式的优缺点。
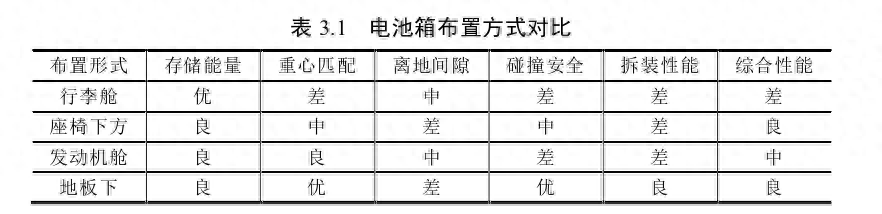
除了集中式的电池布置形式,还有分散式的布置形式。
这主要是因为车辆空间的制约,在保证续航里程的条件下,不得不在多处采用不规则形状布置电池。如图3.1所示的大众e-Golf采用“土”字型的电池组布置形式。
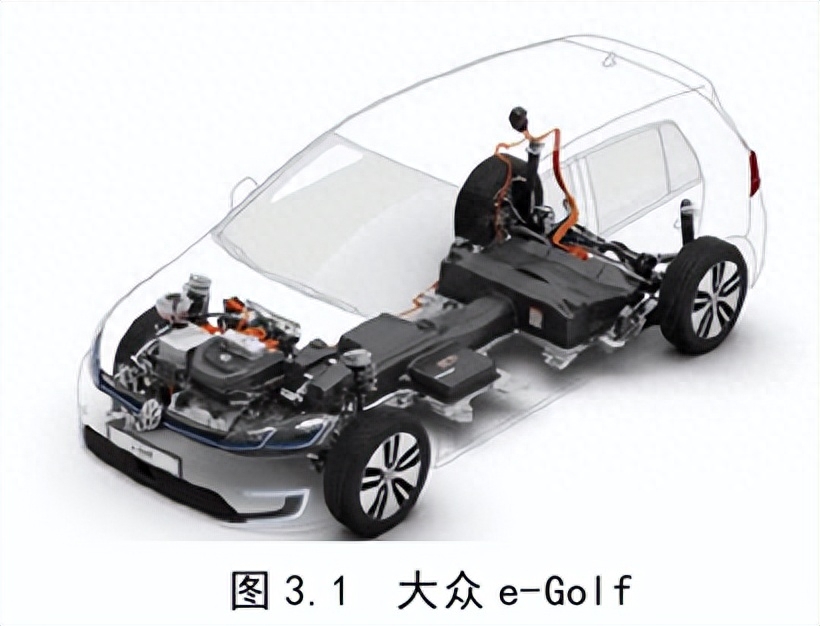
如图3 .2所示的雪佛兰沃蓝达采用“T',字型的电池组布置形式。
尽管电池箱的形状多种多样,布置位置也不尽相同,但是将电池箱布置在地板下比其他位置有更突出的优点。
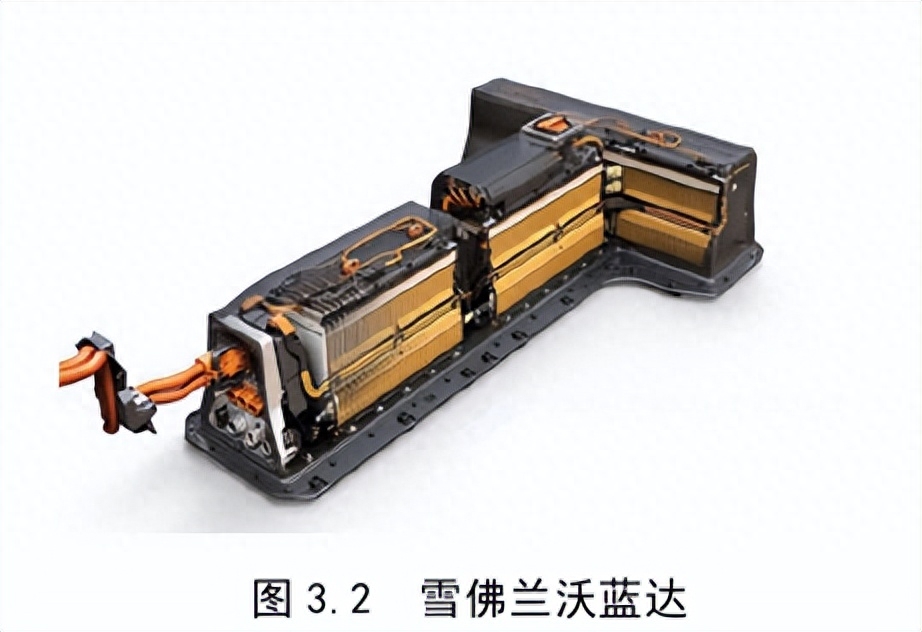
从后期维护和车辆稳定性的角度出发,电池箱不应有过于复杂的形状,以近似矩形为最佳的结构设计方案。
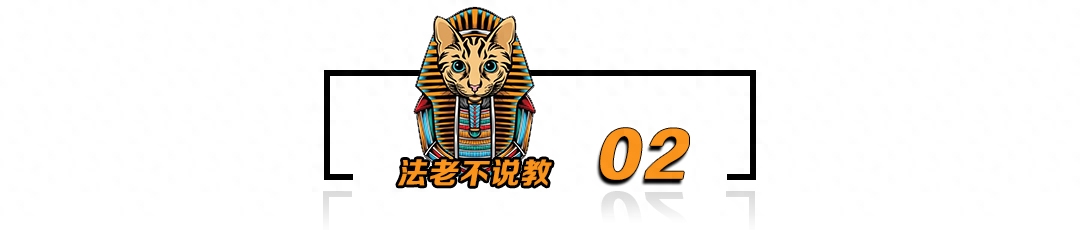
电池箱作为电动汽车能量系统的主要部件,它的性能对电池系统的安全性和整车的稳定性有着重要影响。

正确的仿真工况是评价电池箱性能好坏的前提,本文综合国内外电动汽车电池箱的研究现状和电池箱实际的工作载荷,确定出以下五种典型工况:
(1)颠簸路面转弯
汽车行驶在不平整路面转弯,是典型的常见工况。在该工况下电池箱不应该发生较大变形,以免电池在电池箱内窜动。

同时,若电池箱发生较大位移,电池箱内的线束以及其他附件也会受到挤压,这对汽车能量系统的安全性是不利的。
(2)颠簸路面制动
与颠簸路面转弯工况类似,颠簸路面制动也是常见工况。

(3)模态分析
汽车在工作状态下,由于风载和路面激励的存在,汽车一直处于振动状态。
电池箱的设计应该保证其低阶模态高于汽车的激励频率,从而避免电池箱在外界激励作用下发生共振。

电池箱的共振会影响电池的安全性,也会大大降低电池箱的使用寿命,对整车舒适性也存在负面影响。
(4)随机振动分析
结构在不确定的连续载荷激励作用下,其振动规律是无法用确定的函数来描述的,只能从统计学的角度出发。

以概率来描述,这种振动称为随机振动〔汽车行驶在凹凸不平的路面上,近似于随机振动,所以有必要对电池箱进行随机振动分析。
(5)挤压分析
汽车发生碰撞时,电池箱会受到严重挤压。如果电池箱刚度不足,就会发生较大变形,从而挤压电池。

电池发生较大变形时,有可能导致电池燃烧;同时电池箱被严重挤压时、会发生破裂,电池的化学液体有可能进入乘员舱,危害人体安全。
(1)颠簸路面转弯工况
汽车正常行驶的工况十分复杂,为了能够清晰的描述电池箱的基本性能,通常确定几种典型工况进行分析。

颠簸路面转弯行驶是典型工况之一,电池模组在惯性力的作用下,会给电池箱传递较大的载荷,本文中转弯产生的加速度为0.8g,颠簸产生的加速度为2g。
原电池箱是通过吊耳与车架相连接的,所以在仿真中,需要约束吊耳螺栓孔周围节点的平动和转动自由度。

为了模拟电池模组惯性力的作用,给予电池模组所有单元节点施加相应的载荷。
颠簸路面转弯工况下,原电池箱的位移云图如图3.5所示,最大位移为1.76mm,发生在电池箱的底部中心位置。

一般情况下,当取颠簸路面产生的加速度为2g时,最大位移不超过2mm,所以位移满足要求。
应力云图如图3.6所示,最大应力为22.34MPa,发生在电池箱的底部边缘位置,应力远小于材料的屈服应力,材料利用率不高。
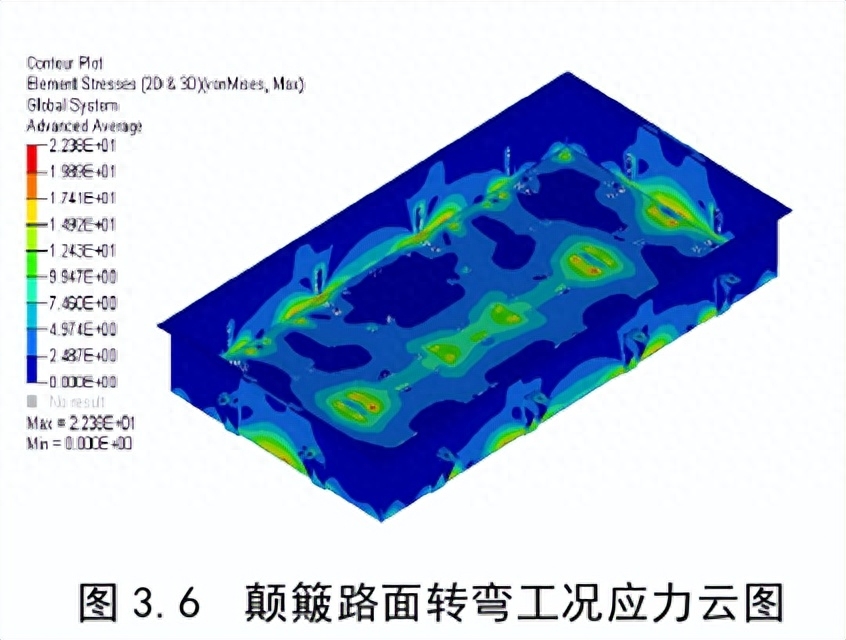
(2)颠簸路面制动工况
颠簸路面制动工况的仿真过程与颠簸路面转弯工况类似。
颠簸产生的加速度为2g,制动产生的加速度为1g,约束吊耳螺栓孔相应节点的转动和平动自由度,加速度产生的作用力施加在电池模组的单元节点上。
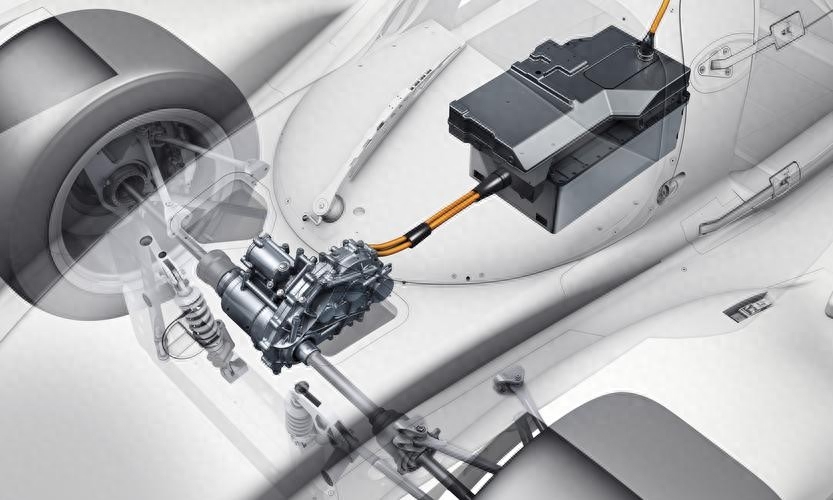
颠簸路面制动工况下,原电池箱的位移云图如图3.7所示,最大位移为1.61mm,发生在电池箱底部中心位置。
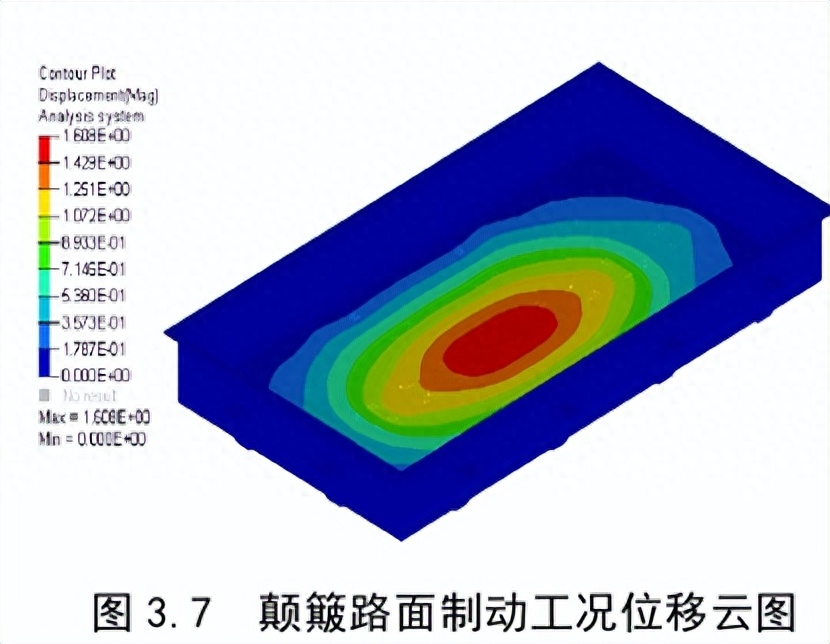
制动工况下的最大位移与转弯工况要求相同,所以位移满足设计要求。
应力云图如图3.8所示,最大应力为22.1MPa,发生在电池箱的底部边缘位置,最大应力远小于材料的屈服应力,安全裕度过大。
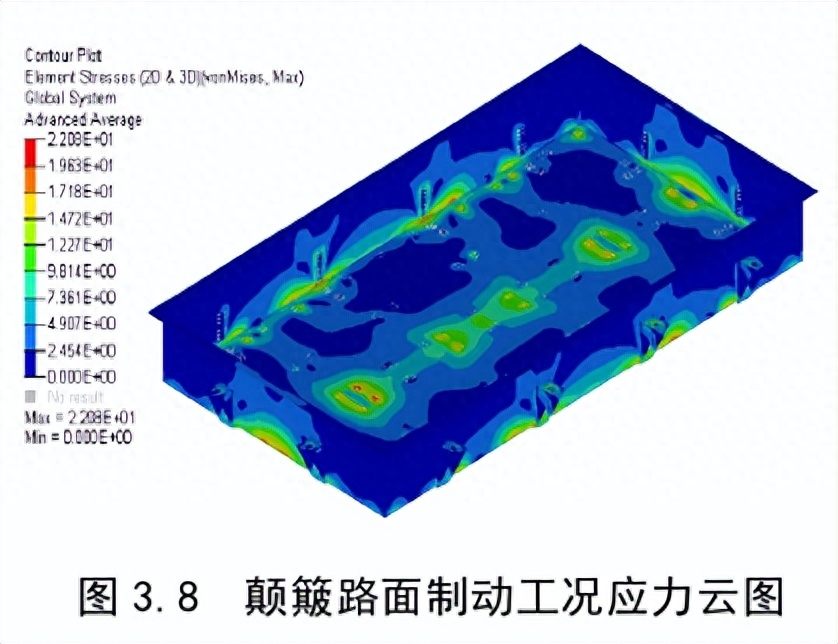
(3)模态分析
模态分析在机械振动领域应用广泛,通过模态分析可以得到构件的固有振型以及各阶频率。
一般情况下,模态存在自由模态和约束模态两种形式,自由模态能够反映构件的整体振动特性,约束模态更与实际贴合。

为了更客观的反映电池箱在实际中的振动特J性,本文所研究的模态均为约束模态。

因为原电池箱是通过吊耳上的螺栓孔和车架相连接的,所以在计算电池箱的约束模态时,需要约束吊耳螺栓孔节点的自由度。
电池箱的前六阶模态频率如表3.4所示,模态振型如图3.9一3.14所示。
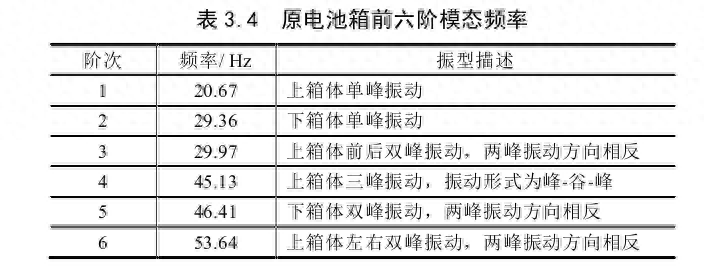

模态分析的目的就是为了避免低阶频率与激励频率重合,从而改善构件的振动特性。
工程中一般采用提高低阶频率的方法来避免共振,电池箱如果在工作状态中发生共振。
电池寿命、结构疲劳、整车舒适性等都会受到严重影响。

电动汽车的主要激励源是电机的振动和路面的颠簸,电机的振动频率一般不超过25Hz;路面的激励频率与路面不平度和车速有关。
波长的关系为:


其中,Y为汽车的行驶速度,L为路面的波长,f为激励频率。我国各种路面不平度的统计参数如表3.5所示。

电动汽车主要行驶在路况良好的道路上,即平坦路面,取行驶车速为1 OOkm/h,平坦
路面的波长为1.0m,根据式(3.1)得到路面激励频率为:
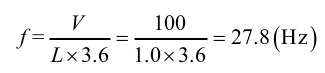
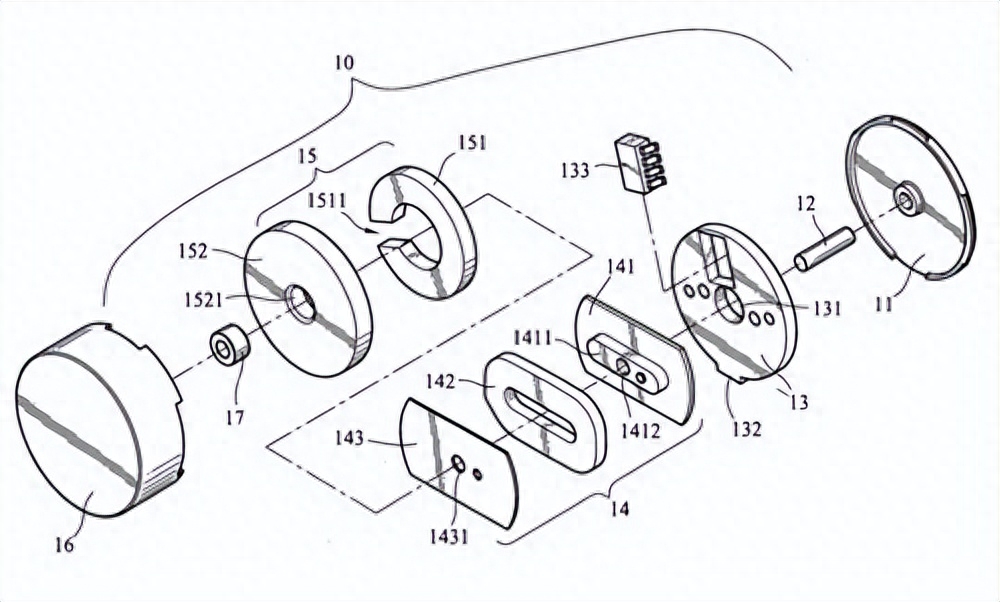
根据以上分析可知,路面的激振频率在30Hz以下,所以,为了避免汽车电池箱在汽车行驶时发生剧烈振动,要求电池箱的一阶频率高于30Hz。
文中的电池箱第一阶模态频率为20.67Hz,小于30Hz,所以需要提高电池箱的模态频率来改善结构振动特性。

(4)随机振动分析
由于路面高低的不确定性,电动汽车在行驶过程中受到的路面激励也是不确定的,所以无法用确定的函数来描述载荷,只能在统计意义上研究。
随机振动分析从统计学的角度出发,是研究结构在不确定载荷下振动特性的有效方法。

通过随机振动分析可以预测结构的疲劳寿命,所以对电池箱进行随机振动分析是十分重要和必要的。
根据国标GB/T 31467.3-2015中的相关规定,需要对电池箱的三个方向进行随机振动测试。

各个方向的功率谱密度曲线如图3.15所示,如果电池箱安装在乘员舱下部,测试参数按照表3.6、表3.7、表3.9进行。
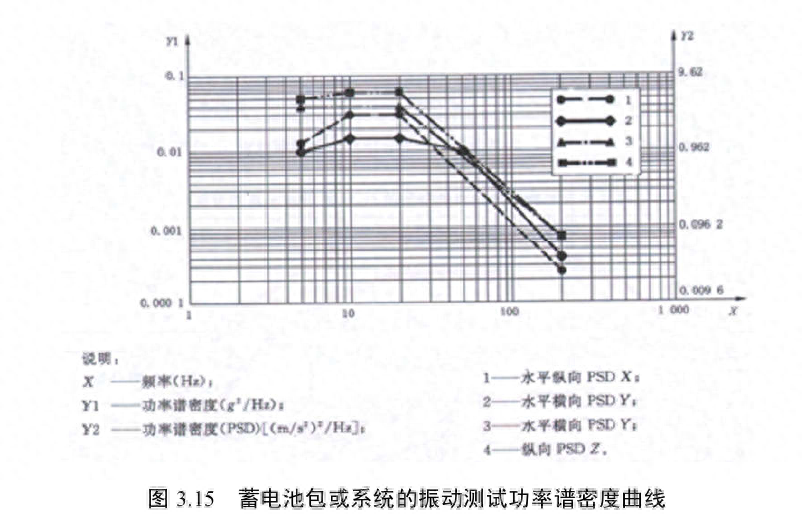
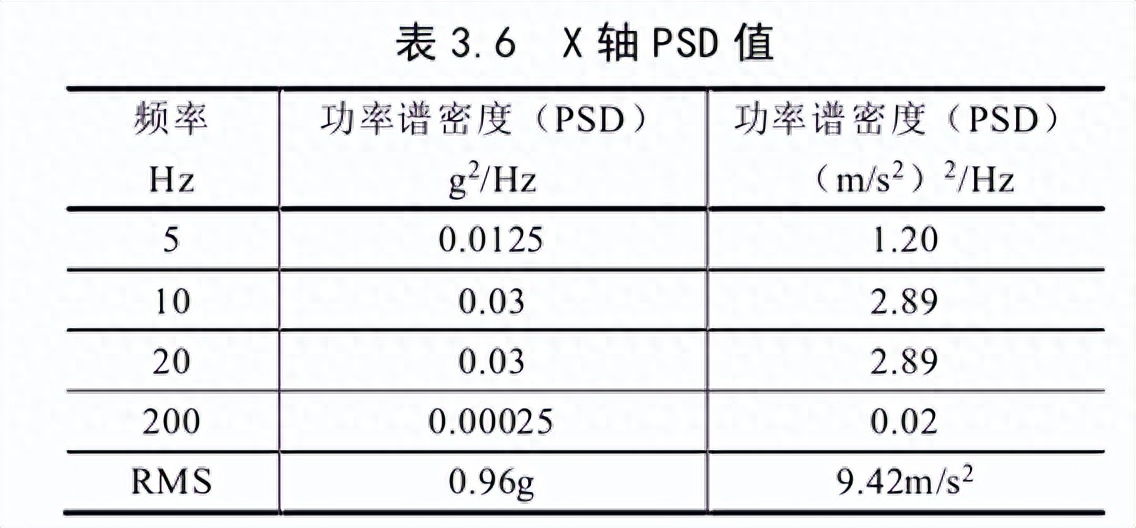
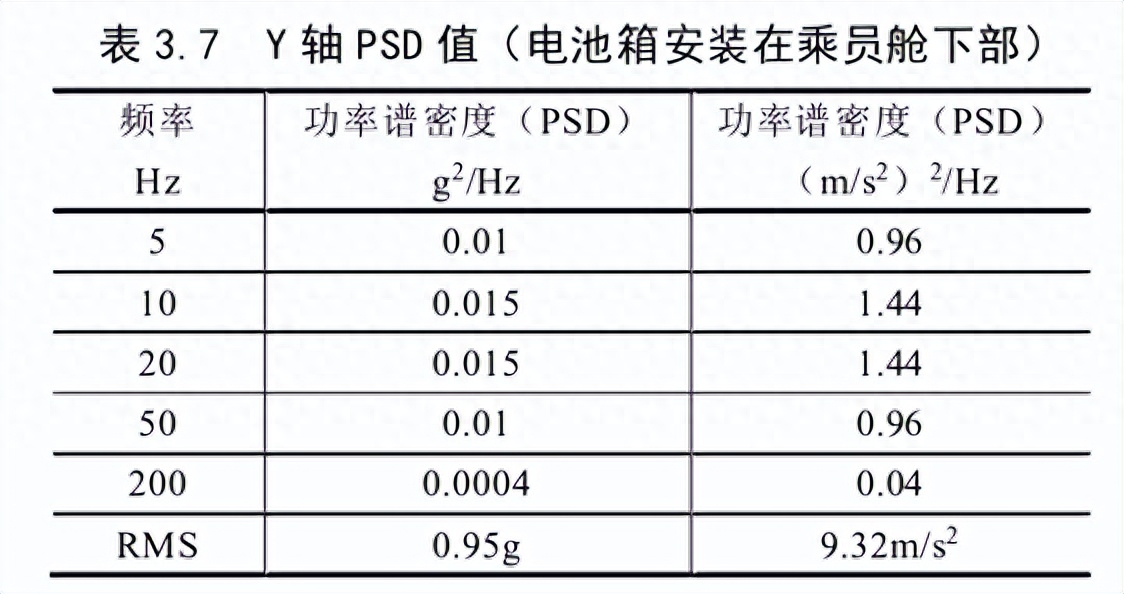
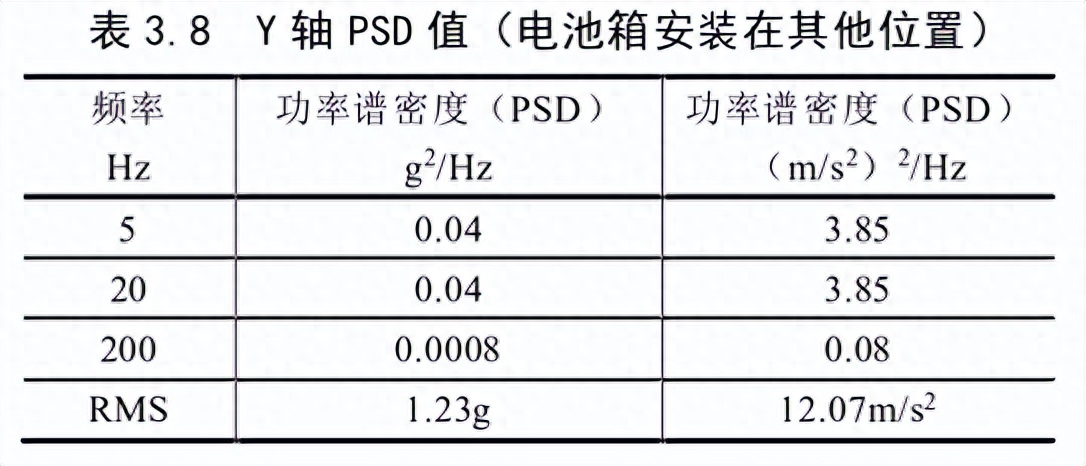
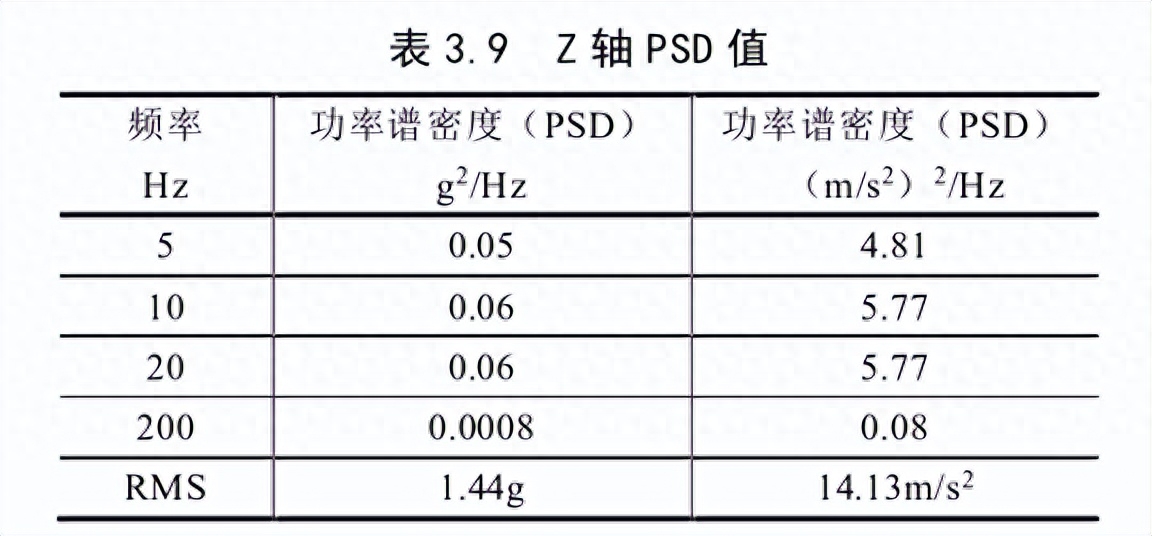
如果电池箱安装在其他位置,测试参数则按照表3.6、表3.8、表3.9进行。
本文所研究的电池箱安装在乘员舱下部,所以测试参数按照表3.6、表3.7、表3.9进行。

根据电池箱在振动测试台上的固定方式,利用RBE2单元将吊耳螺栓孔节点相连,这样就可以直接在RBE2单元的中心节点上进行加载,同时也有利于后处理结果的查看。
随机振动仿真建模借助Optistruct软件中的Random PSD Frequency Response向导完成,采用模态叠加法进行随机振动求解。
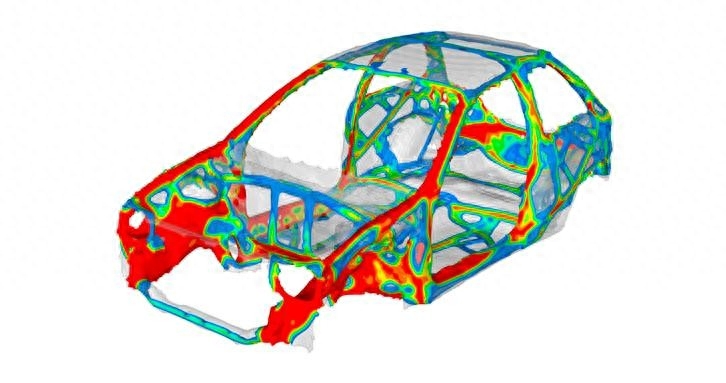
为了验证仿真的正确性,可以对比加载节点的载荷功率谱曲线与响应功率谱曲线是否一致,因此,本文列出了X, Y, Z向加载点的响应曲线。
分别如图3.16、图3.18、图3.20所示,图中激励点的响应曲线与加载曲线完全一致,说明随机振动仿真分析是正确的。
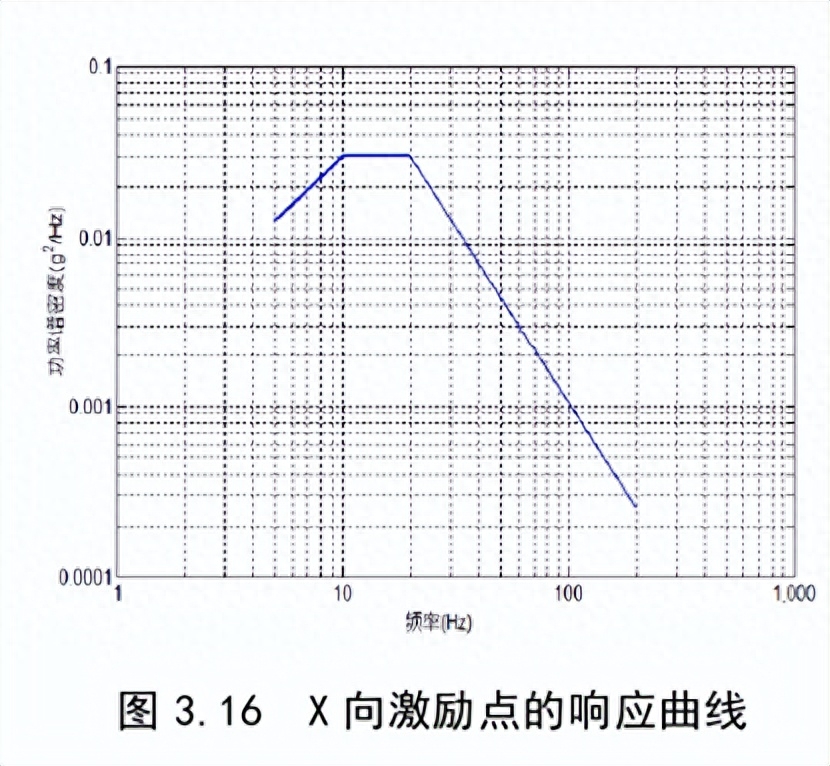


X, Y, Z三向的1二应力云图分别如图3.17、图3.19,图3.21所示。X向最大1二应力为10.7MPa,发生在吊耳螺栓孔处,对应的3二应力为32.1MPa;。

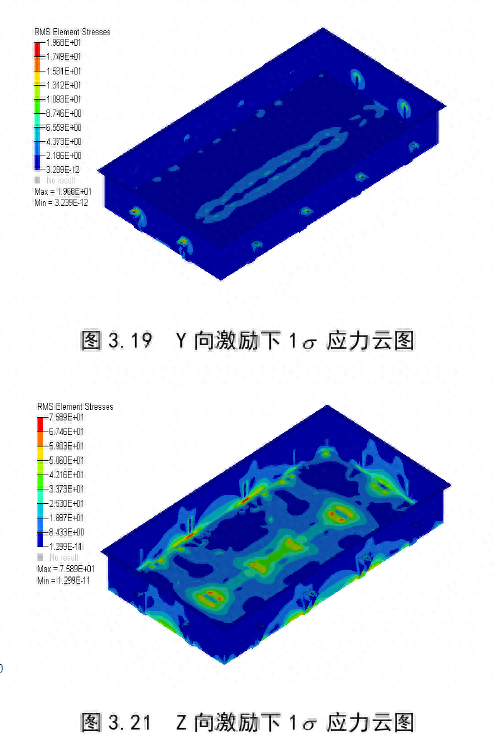
Y向最大1二应力为19.7MPa,也发生在吊耳螺栓孔处,对应的3二应力为59.1MPa; Z向最大1二应力为75.9MPa,发生在下箱体边缘位置。
对应的3二应力为227.7Mpao X, Y, Z三向最大3二应力均小于材料的屈服应力,说明电池箱在X, Y, Z三向的随机振动载荷下,均能满足安全性要求。

(5)挤压分析
汽车行驶过程中难免发生事故,在发生剧烈碰撞时,电池箱会受到严重挤压。
如果电池箱没有一定的防撞能力,电池会受到过度入侵,轻则电池系统破坏,重则电池破裂、化学物质泄漏、伤害乘员。
所以电池箱的防撞性能对能量系统来说相当重要。
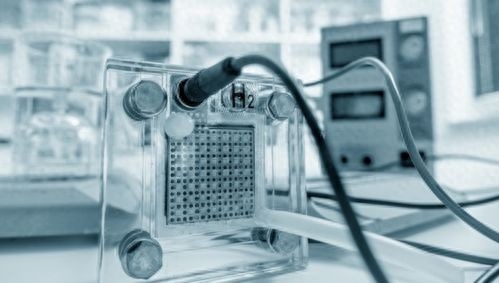
国标GB/T 31467.3-2015中说明了电池系统的碰撞、挤压测试方法,但是所述的测试方法主要关注的是电池的安全性,没有评估电池箱结构变形的相关内容。
因此,本文参照国标的测试方法以及与主机厂进行商讨,提出了新的挤压分析工况和评价指标。
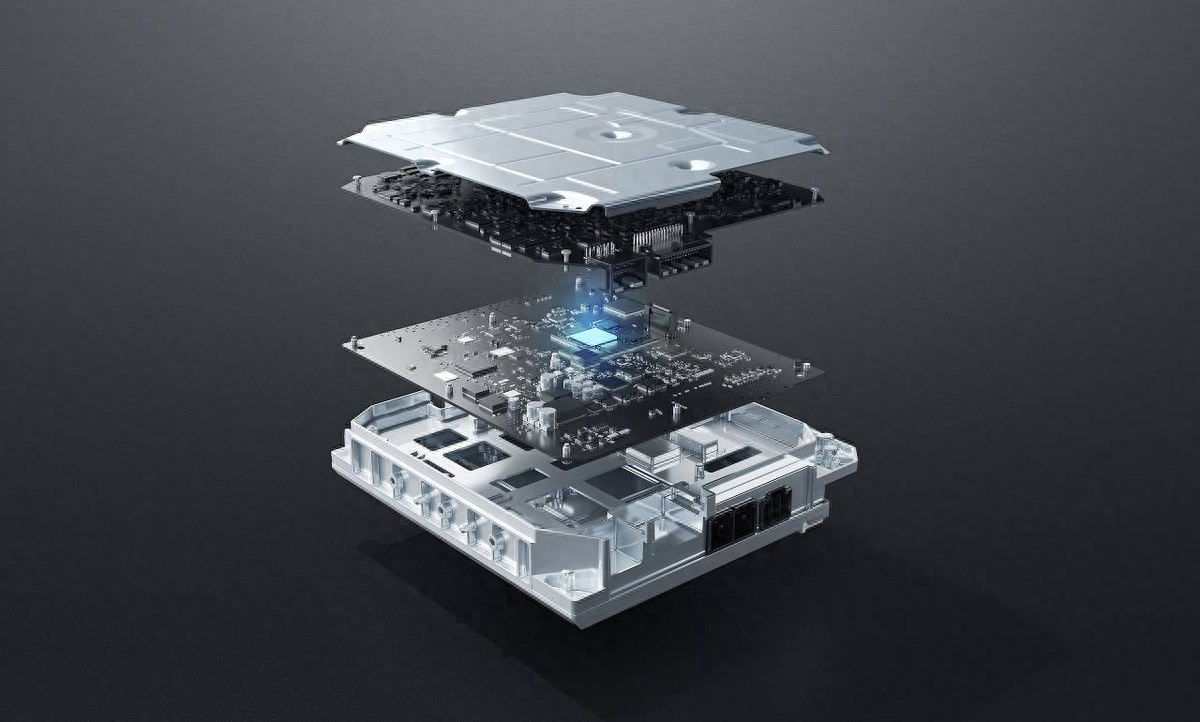
(6)横向挤压
施加在电池箱左右侧面的挤压力为15kN,电池箱在变形后不应该侵入电池,且箱体不发生破裂。
(7)纵向挤压
施加在电池箱前后侧面的挤压力为15kN,电池箱在变形后不应该侵入电池,且箱体不发生破裂。
按照本文所提出的测试方法对原电池箱进行横向挤压和纵向挤压仿真,载荷以均布力的方式施加在对应单元的节点上。

横向挤压工况下的位移云图如图3 .22所示,最大位移23.76mm,出现在上箱体的中心位置,下箱体侧面最大位移为Smm。
上箱体与电池之间的距离为3 Omm,与车身之间的距离为20mm。

下箱体左右侧壁与电池之间的距离为20mm,所以在横向挤压工况下,原电池箱的变形对电池没有侵入,但上箱体变形量过大。
横向挤压工况下的应力云图如图3.23所示,最大应力为352.6MPa,发生在上下箱体的连接位置,小于材料的强度极限,可认为原电池箱不发生破裂。
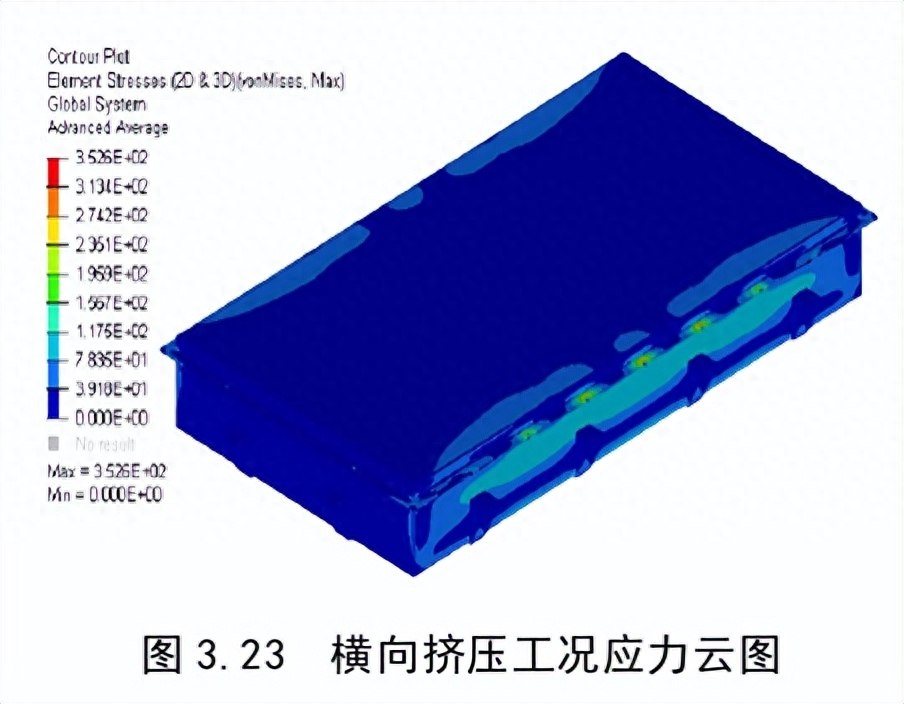
纵向挤压工况下的位移云图如图3 .24所示,上箱体的最大位移为10.39mm,下箱体侧面最大位移为6mm。
下箱体前后侧壁与电池之间的距离为3 Omm,所以在纵向挤压工况下,原电池箱的变形对电池也没有发生侵入。

横向挤压工况下的应力云图如图3.25所示,最大应力为242.2MPa,出现在下箱体的挤压位置,小于材料的强度极限,可认为原电池箱在纵向挤压工况下不发生破裂。
虽然横向挤压和纵向挤压均满足设计要求,但是横向挤压工况下最大应力过大,存在连接位置材料破损的风险,所以需要优化挤压工况下的应力分布。

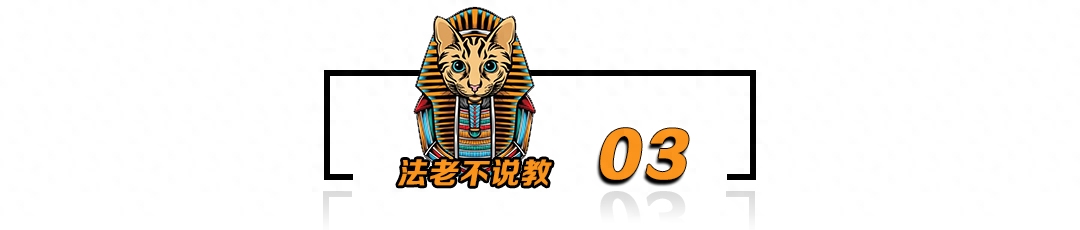
本文首先介绍了电池箱的结构设计概述,接着对某车型的电池箱进行测量,获取相关参数,并在CATIA软件中建立了原电池箱的几何模型。

在Hypermesh软件中建立原电池箱的有限元建模,然后,根据国内外对电池箱的研究现状,确定了仿真工况,并提出新的挤压仿真工况和评价指标。
通过对原电池箱进行仿真得到各工况下的性能响应,并对各工况下的性能做出评价。本章的仿真工况和分析结果为后续电池箱优化提供了设计基础。
参考文献
(1)吴琼.碳纤维轿车保险杠横梁的设计[D].武汉理工大学,2014.
(2)薛姣.碳纤维复合材料汽车B柱简化结构参数分析[D].中北大学,2013
(3)吴方贺.碳纤维复合材料发动机罩结构设计与优化[D].吉林大学,2017.
(4)潘玲玲.碳纤维复合材料典型车身覆盖件设计开发与试制[D].同济大学,2006.
《封神》打脸流水线古偶剧,真发、真骑术拉高观众对古装剧的要求
电影《封神》异军突袭,无数网友自愿充当“自来水”!明代小说《封神演义》以殷商为背景,讲述武王伐纣的故事。《封神演义》被多次影视化,“锁锁”、马景涛版,温碧霞、陈浩民TVB版,林心如版,曹骏、罗海琼版等等。再度翻拍经典IP,难度系数可想而知。套路网2023-08-07 11:45:030000知名鸭脖企业号自曝使用大量添加剂?相关公司回应
近日,“曹氏鸭脖”的企业认证号曝光了自家汤料的配方,里面含辣汤香精、油溶性辣椒精等十多种添加剂,并以前员工的口吻称这是蜀湘曹氏鸭脖公司的配料。9月7日,蜀湘曹氏鸭脖所属公司就此事回应称,该账号和“前员工”与公司无关,是有人恶意诋毁。辖区市监局回应称,他们会记录并了解此事。“曹氏鸭脖”企业号自曝加多种添加剂套路网2023-09-08 20:04:4300008月29日下午,有四位学校校长被查落马,触目惊心。看看都有谁?
反腐倡廉,国家一直都非常重视,及时彻查出贪腐官员,百姓都会拍手叫好,这不仅能推进社会的和谐发展,更能提升百姓生活的幸福感,可谓是一举两得。两会以来,我国反腐持续输出,希望在职的官员,一定要遵守党的宗旨,全心全意为人民服务。医院、学校已经成为了反腐重地,一定要引起国家的高度重视,都与老百姓息息相关,反腐势在必行!两会以来,在国家的带领下,我国反腐倡廉进入常态化普遍化。套路网2023-08-30 18:54:490000投资矿石?一男子因诈骗获刑8个月
极目新闻记者赵贝通讯员冉利咸杨露9月8日,极目新闻记者从湖北恩施利川市人民法院获悉,该院近日审结一起诈骗罪案,被告人以矿石投资为幌子,诈骗投资人钱财,最终被判处有期徒刑八个月,缓刑一年,并处罚金人民币2000元。套路网2023-09-10 13:57:430000多病原叠加下儿童如何正确防治呼吸道疾病
来源:【中华泰山网】当前,随着我国各地陆续入冬,呼吸道疾病进入高发时期。据了解,近期,我国呼吸道感染性疾病以流感为主。此外,还有鼻病毒、肺炎支原体、呼吸道合胞病毒、腺病毒等病原引起。儿童为何更容易出现多种呼吸道病原体叠加?儿童患者是否都需要进行多种病原体检测?如何正确防治呼吸道疾病?武汉市金银潭医院感染科与急诊科专家就此作出解答。0000